Of drilling towers and thermal springs | Improving resilience by saving energy in BSH Nazarje
5 minutes
Normally, we associate thermal springs with recreational stays. At our production site for small appliances in Nazarje, things are quite different. There, BSH harnesses thermal springs through the drilling of 14 boreholes. Not for sauna bathing, but to make the site self-sufficient in energy. With success.
Have you ever been to Nazarje? It is a small, dreamy town in the north of Slovenia. Characteristics of Nazarje is both the beautiful river Savinja and the mountain scenery, which frame the town and merge it with nature.
Nature is also a keyword that has a very special meaning for our BSH production site in Nazarje. Here, around 2,000 employees manufacture small home appliances for food and beverage preparation, such as blenders, and kitchen machines. It is also the home of our beloved Bosch Cookit and our Bosch SmartGrow Life.
"The story sounds really breathtaking, but there are also many years of hard work in the project. So it's not like someone just pushed a button."
- Jože Zamernik, Project Manager.
The site has developed vigorously in recent years. Between 2010 and 2021, the number of employees increased by 71 percent, and the production volume by 48 percent. Despite this, our factory in Nazarje has managed to significantly reduce electricity (-59 percent) and water consumption (-39 percent) as well as waste (-12 percent) per t/product.
At the same time, Nazarje has also gradually moved toward energy self-sufficiency in recent years, making itself less dependent on the energy market. Just a few years ago, around 20 percent of the site's total energy consumption was used for heating and cooling alone. Now, instead of 2,000 MWh of energy, only 460 MWh of energy is needed each year. This has been achieved through a whole series of measures. Particularly noteworthy, however, is the use of geothermal or thermal heat, which makes a massive contribution to energy savings.
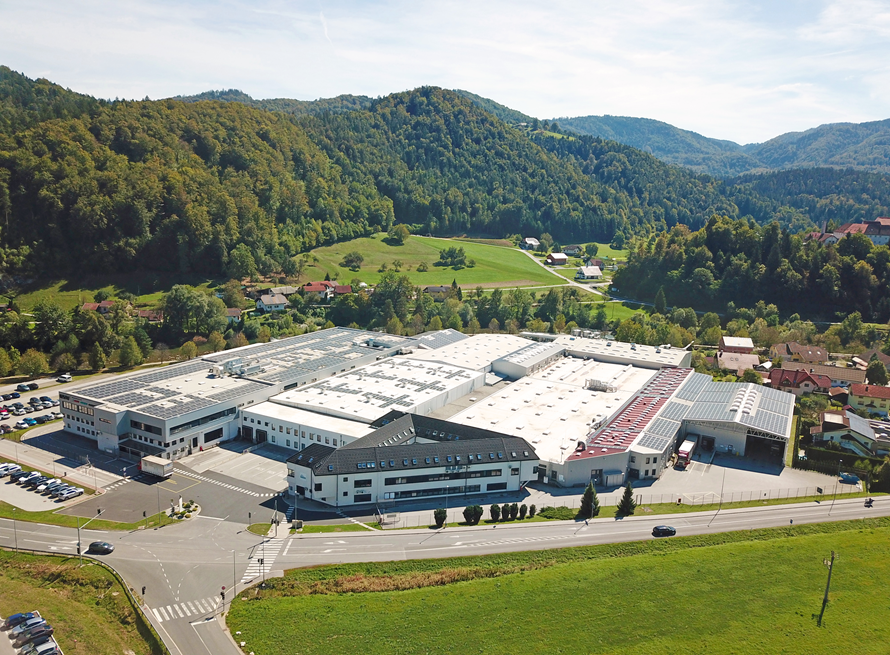
What exactly was done at the site?
Between 2011 and 2020, a total of 14 boreholes were drilled into the ground at depths of between 14 and 30 meters, where thermal springs with a temperature of around 14 degrees Celsius are located.
BSH is making use of these. Using a heat pump, the thermal springs’ water temperature is absorbed and compressed. This generates a lot of additional heat, which is transferred to a heating tank. In this way, the heat can be retrieved at any time, for example, to ensure warm hands and a good mood on the production lines in the fall and winter. By transferring the heat energy to another medium, the heat pump cools down so much that it is cold enough again to absorb the heat from the thermal springs. The process thus starts again from the beginning.

Thus, since project completion in 2020, the heating system can be operated completely self-sufficiently, so without additional energy. In addition, the newly installed heat pump system is also used to utilize heat that is generated as a "waste product" during the plastic injection. Each year, this saves around 1.6 GWh of heat energy. In addition, the site requires 350 MWh less electricity each year.
As we use the thermal heat for cooling the machines and surroundings in the summer we have less chiller demand. Thus, we need less maintenance and fewer future investments in chillers.
At the same time, it is now also ensured that it is pleasantly cool on the production lines in summer. Until a few years ago, there was no cooling system, which meant that many employees had to work in a sweaty environment. Thanks to this new, closed circuit for cooling water, an additional 2,700 m³ of drinking water can be saved annually.
Thanks to this new, closed circuit for cooling water, an additional 2,700 m³ of drinking water can be saved annually.
The result is a sustainable form of energy generation, cost savings, and greater comfort for employees. But what is the catch?
When asked about this, Jože Zamernik, the Project Manager, has to laugh at first. "The story sounds really breathtaking, but there are also many years of hard work in the project. So it's not like someone just pushed a button." The core team from Nazarje worked for total of nine years on this project with support from external specialists.
"During an investigation of the groundwater at that time, we had determined that we could use its thermal energy potential for our heat supply. So we had to drill a total of 14 boreholes in the vicinity of the factory. We also wanted to use the waste heat from the injection molding machines. With our project, we found a way to combine the two to supply the entire site with thermal energy on a self-sufficient basis since 2020," explains Jože.
Spurred on by the great success of the project, the colleagues in Nazarje have already set themselves the next, ambitious goal: By 2025, the entire site is to be operated CO2-free - entirely without the need for compensation certificates. Here, the goal of installing additional photovoltaic systems with 510 kWp in 2023 also pays off. As a result, a total of around 15 percent of the site's electricity would then be self-produced.
These efforts are part of global BSH projects that tackle the topics of energy efficiency and reducing CO2 emissions. The colleagues in Nazarje are very active here and share their takeaways with all BSH sites around the world.