What Nanjing's Heat Recovery Has to Do With CO2 Neutrality
All BSH locations worldwide have been operating CO2-neutral since late 2020. One component of this success: less energy consumption in production! To achieve this, BSH colleagues in Nanjing, China, are relying on waste heat recycling. Find out how it works now!
Our 32,000 m² laundry care factory in Nanjing produces around 1.5 million appliances a year. Consequently, the location needs about 16,845 MWh of energy per year – five percent of which is used to heat office and factory premises. This is roughly equivalent to the annual consumption of 300 three-person households in China. In order to reduce this number, Senior Engineer Wu Pengfei and his team looked into the possibility of recycling heat from production in 2019. This is because many mechanical processes are generating wasted heat, for instance, air compressors. They draw in air from the environment and compress it, similar to a bicycle pump. The compression generates pressure, which in turn generates heat energy. While the compressed air’s pressure drives screwing processes in the production plant, for example, the heat previously remained unused and was emitted to the outside in the form of steam via fans.
"To change that, we equipped the compressors with heat exchangers in April 2020," explains Pengfei. The biggest challenge here: installing the new system without interfering with ongoing production. That is why the installers worked mainly at night and on non-production days. They also kept backup solutions on hand to ensure that the equipment could continue to operate. Among others, the team always kept one air compressor running to make sure that are no production breaks.
"I really enjoyed coordinating the installation of the heat exchangers with various business areas, and I'm proud that we can save so much energy as a result," Pengfei emphasizes.
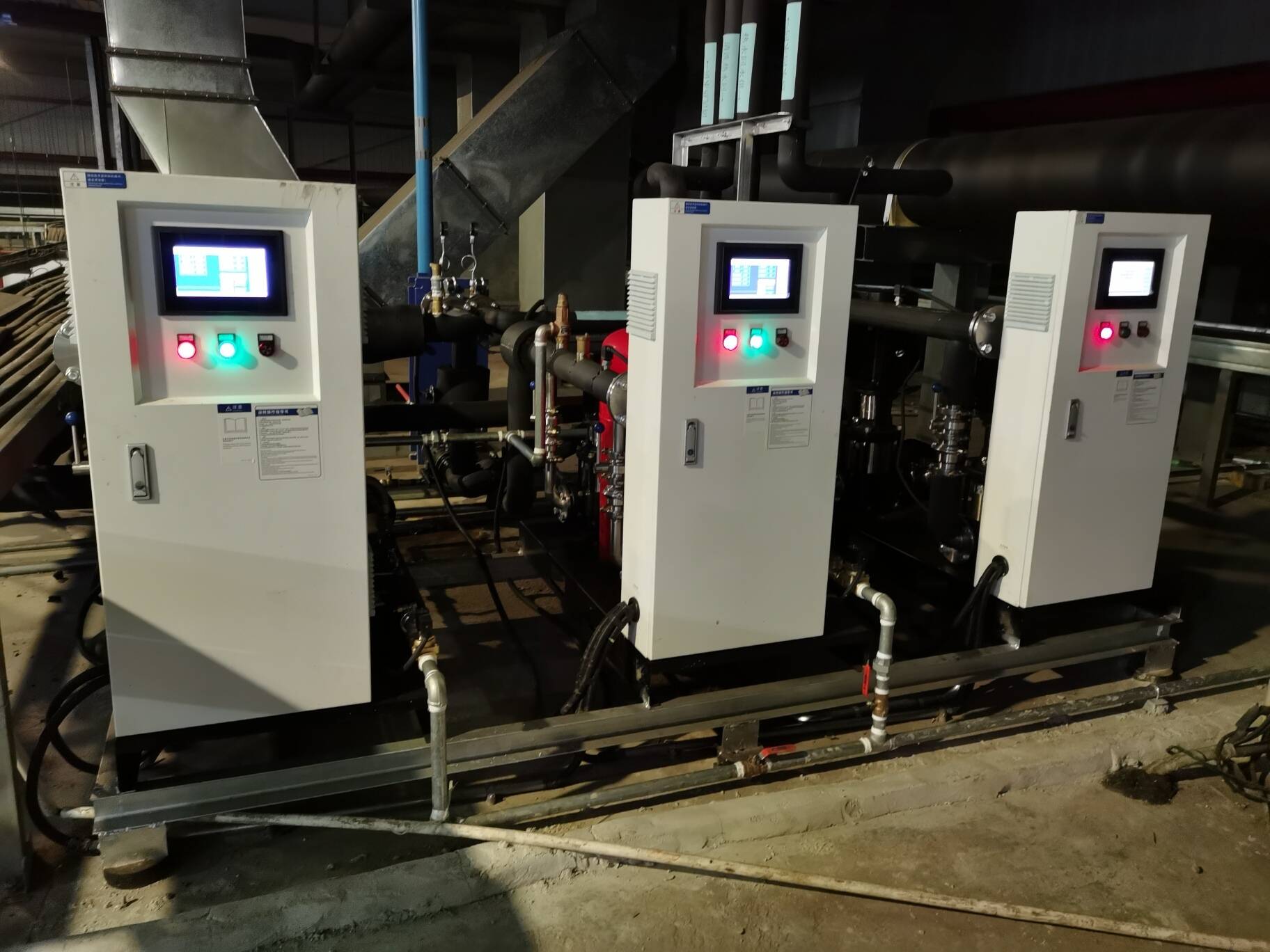
The heat exchangers transfer waste heat from the compressors to a closed water circuit.
Waste heat as an energy source
The heat exchangers transfer thermal energy from one system to another. In this way, the waste heat from the compressors becomes an additional source of energy. Stored in a closed water circuit, the recovered heat now heats a local degreasing machine. The latter requires water heated to around 55 degrees Celsius for cleaning metal sheets. "The heat for this was generated with electricity before the transformation. Now, we don't need the electricity for this machine any longer because we tap the heat source directly," Pengfei continues. Even better, there is enough heat left over for heating 1,600 square meters of workspace. With the help of this clever recycling solution, the team saves more than 728 MWh in electrical energy and 520 tons of steam annually. Saving this energy was an important component of ensuring that all BSH locations worldwide become CO2-neutral in 2020 – because less energy consumption also means less CO2 emissions.
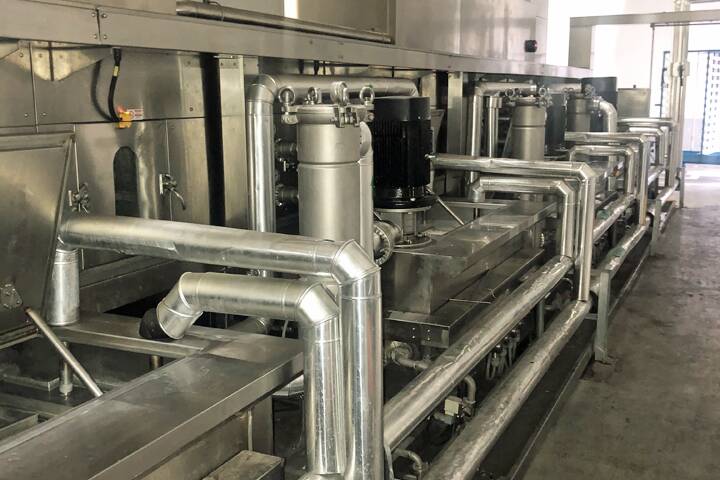
The leftover heat from the air compressor is used to heat the water in the decreasing machine.