Autonomous Mobile Robots Work in the Rzeszów Factory
Reading time for this article: 8 minutes
Autonomous Mobile Robots (AMR) now zoom around the Rzeszów factory as the latest solution in the market for system automization and the next step in making employees' work easier. Anna Jonkisz, Leader of the vehicle launch project, and Radoslaw Kitka, Head of the logistics department, run us through how this works.
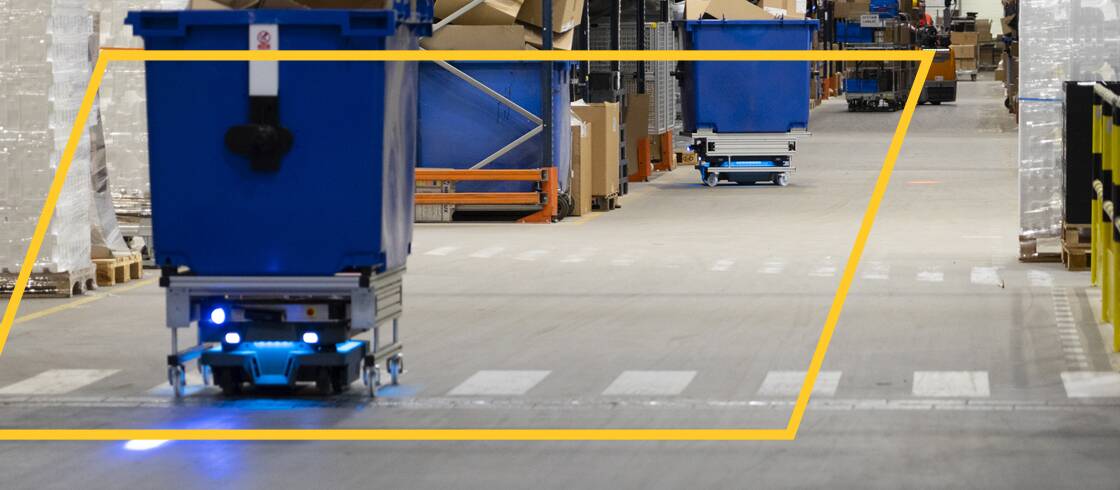
Progression of automation in the Rzeszów factory
Containers were once pulled by “tugger-trains”, and operated via the aptly named milk-run system where an operator had to go the warehouse, hook up the containers filled with waste to the tugger (2-3 containers attached as a milk-run system), drive them to the collection area, hook up the container to the tipper, unhook the container, and take the empty containers to the warehouse. Today, this work is fully automated.
Initially the team was considering the implementation of vehicles that move along marked paths. “However, we came to the conclusion that in Rzeszów we should use the most modern solution of this type, i.e. AMR (Autonomous Mobile Robot). The robots “replace the manual work of operators, allowing their potential to be used in other, more complex storage operations” says Anna. More specifically, two autonomous vehicles pick up containers filled with waste paper, like cardboard packaging for materials from the warehouse, and transport them to the crushing press.
Technically speaking “there are several docking stations at the warehouse, each one with the panel to trigger the robot’s mission. The control light on the panel indicates whether the container is correctly docked in the station and when the container is full, operator needs to push the button on the panel which triggers the mission for the robot” explains Anna.
“The robots perform approximately 100 journeys each day with 1,100 l trolleys over a distance of approximately 200 meters. This is just the beginning of the automation of traffic in the factory” – Radoslaw Kitka, Head of the logistics department at BSH in Rzeszów.
The autonomous mobile robot (AMR) is the latest solution that achieve this as it understands and moves through its environment without being overseen directly by an operator or being limited to a fixed, predetermined path marked by QR codes or painted lines. “They are capable of free-movement and real-time path planning that enables them to collaborate in material handling tasks with humans. They use so-called SLAM technology (Simultaneous Localization and Mapping) which allows the robot to map its environment while positioning itself in it,” elaborates Radoslaw.
At first, the robots were met by factory employees with the expected mixture of healthy skepticism and blossoming curiosity, but “the main goal of implementing autonomous solutions in the factory and warehouse is relieving employees of non-productive tasks, improving work safety and optimizing warehouse costs. Process automation in the future is inevitable and the sooner we are exposed to it and gain the necessary experience, the more competitive we will be,” underlines Anna Jonkisz, Leader of the vehicle launch project.
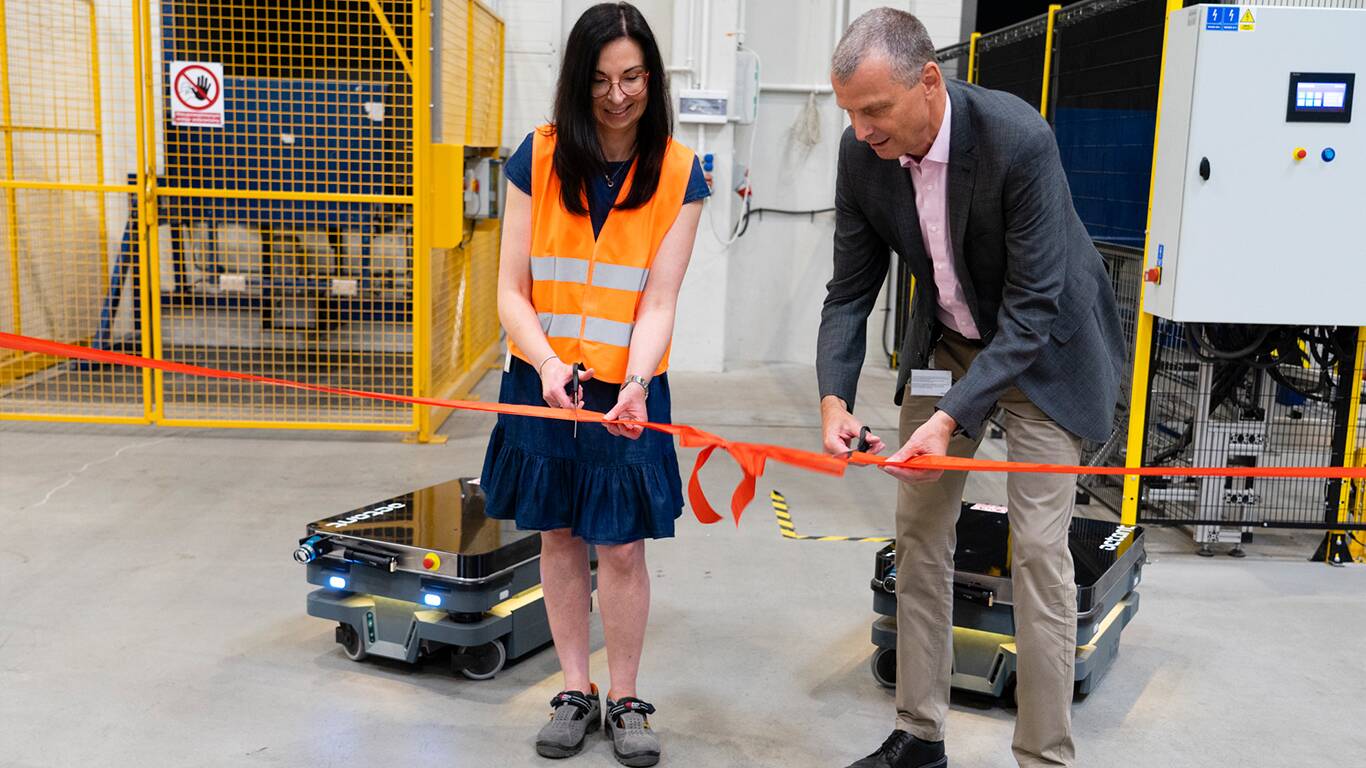
“We dream big, and we want to make a difference, but this is just the first step” - Anna Jonkisz, Leader of the vehicle launch project
Mapping, meeting challenges and finding solutions
Integration is taking form as a collaboration between BSH, automation specialists, and an external company. They were then customized to meet BSH needs.
“We are still in the implementation phase; we constantly observe the robots for emerging problems like correct mapping and we try to eliminate them” explains Anna.
The most important thing is enabling the robots’ correct navigation, which is why correct mapping is essential - robots are very sensitive to any obstacles in their path. For example, even if a skylight casts a shadow on the floor, it becomes a form of obstacle for the robot to avoid.
To navigate properly, robots need fixed reference points, so in some places we need to add them and teach the warehouse staff not to obstruct them with pallets or parked forklifts, otherwise the robots get lost.
In the end, the robots are there to make employees’ lives easier, so the team is figuring out the best case, where employees and the robots have an optimal working environment.
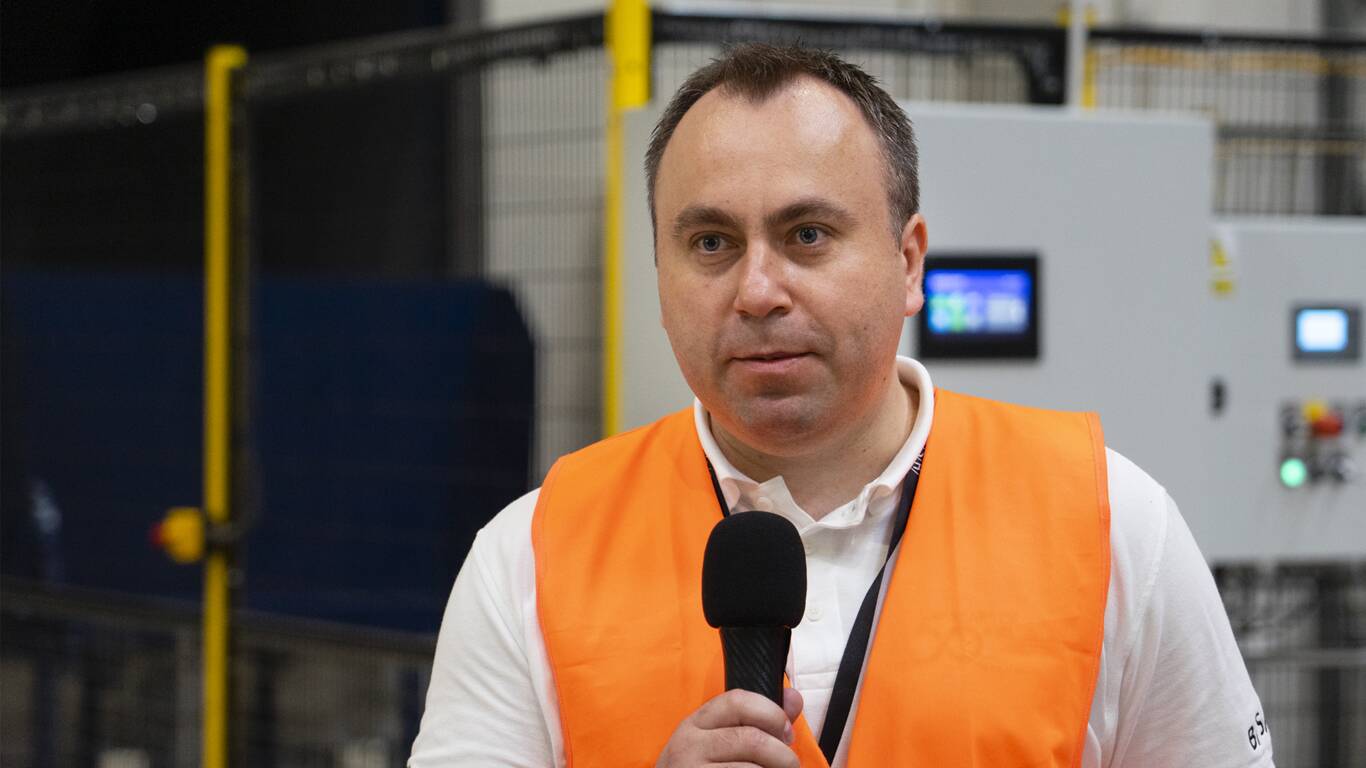
Radoslaw Kitka, Head of the logistics department at BSH in Rzeszów.
The near future of autonomy at the Rzeszów factory
There is a strong drive to continue the investment in robotics wherever it relieves the physical strain on employees and advance automation in a meaningful way.
The Polish team is already planning their next moves. “We want to transport finished goods from the assembly line to the warehouse and transport the materials from the warehouse to the assembly lines as a line feeding, for instance”, adds Anna.
“The main idea is to create a network of automization, where different processes can communicate, like Uber”- Radoslaw Kitka, Head of the logistics department